In the wood pellet production, German company Van Roje was able to raise the production capacity from 60 to 90 tonnes with the same volume of heat and without additional combustion systems. This was possible with Saalasti High-Pressure Dewatering Press 1803 “Hippo”, which removes approximately half of the water content of the wood.
The need to raise capacity and modernise pellet production
Energiepellets Oberhonnefeld, part of van Roje, has specialised in sustainable pellet production since 2007. The company has one of the leading softwood sawmills in Europe with a long company history.
The sawmill produces wood chips and sawdust, which are processed into FSC and EN plus certified wood pellets on the Oberhonnefeld site. The high-quality wood pellets are made only from natural sawdust without artificial binders. The energy for the pellet production comes from the company’s heating plant, which offers renewable energy for production.
Van Roje planned to grow its pellet production from approximately 40 000 tonnes to 80–90 000 tonnes per year. But there was a question about heating and drying capacity and how it could answer to increasing demands of capacity raise. The belt dryer was fully in operation, while the heating plant was close to the upper limit of its capacity.
− The problem was that we did not have enough heat in our heating plant to raise the pellet production volume. And then we heard about the new Saalasti press, says Gerhard Hauschulte, the Managing Director of van Roje.
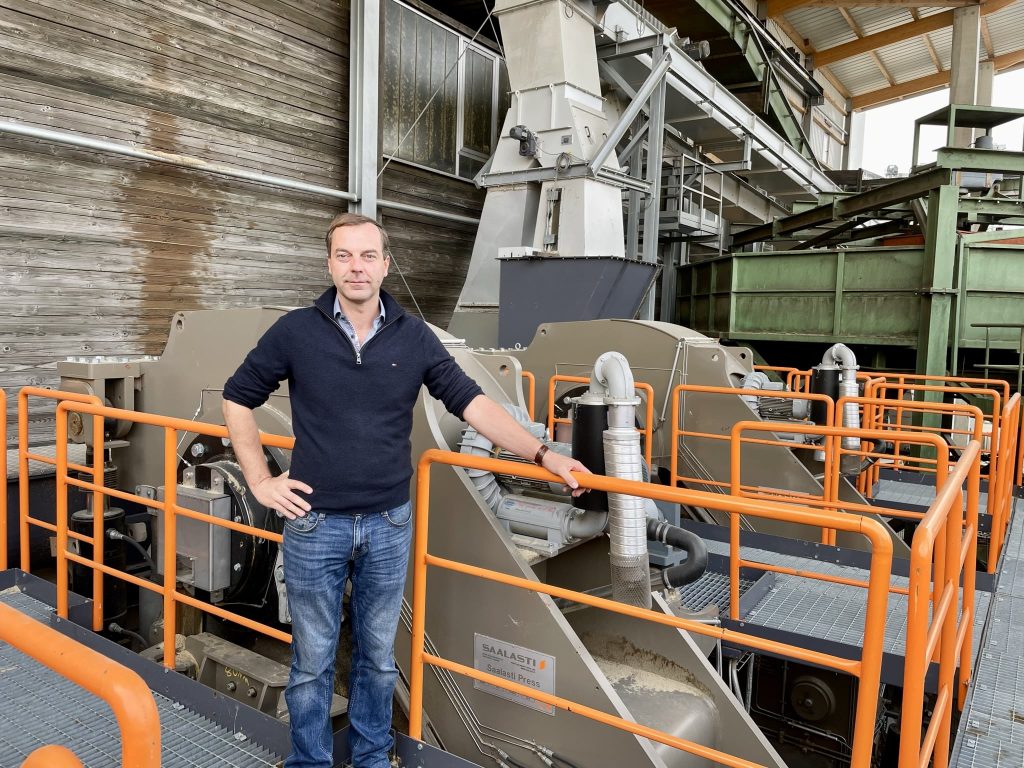
Higher production rate and massive energy savings year-round
The solution to boosting productivity came with the new Saalasti Press 1803, also known as ”Hippo”. The new press is a mechanical dewatering solution, which reduces the moisture content of biomasses such as wood chips and sawdust. The ”Hippo” press is the newest version of Saalasti presses, which have been market leaders many years before.
The benefits of the new technology soon became apparent. The press drastically reduces raw wood’s moisture content while connected upstream of the belt dryer. The water content of the wood that van Roje uses is about 40 % before the drying process.
The press reduces about 55 % moisture from the material, which is a very big improvement.
Thanks to the lower water content of the biomass, the belt dryer’s performance is maximised with the same thermal energy. This meant that van Roje had also gained massive energy savings.
– There was no need to invest in energy production or an additional combustion system. Otherwise, we would have needed a bigger belt dryer, Hauschulte adds.
The moisture removal is so effective that the operation stays steady year-round, which was not the case before.
– Normally, our capacity would be smaller in the winter, but now we can run our operation steadily year-round. Without the presses, we would have about 50 % less capacity in our pellet production, Hauschulte highlights.
Top-quality material with lower pellet production cost
The innovative solution was convincing, as it was tailored to the needs of van Roje, as Hauschulte says.
− It was very important that the solution could be able to press both sawdust and wood chips. Saalasti was the only one who could provide a viable technical solution for the use of sawdust also.
The press also improves the quality of the dry material. The wood chips are pre-crushed in the press, which increases the evaporation surface of the material. The material will thus be more homogenous overall, while the whole thermal drying process will be more efficient.
Press is a long-term investment that will pay itself back in several ways. The machine enables greater capacity while saving energy, and there are continuous savings on the pellet production costs.
The production cost per tonne is much cheaper with the press, while the energy savings are huge.
− I have recommended this solution to several companies with the same operation as us. The heavy construction of the machine is also a good thing, and its operation is very reliable, Hauschulte ends.
The benefits in short
- Higher production volume with the same amount of heat; no need to add energy consumption.
- Removes the moisture content from both wood chips and sawdust dramatically.
- The quality of the dry material is improved in the crushing and drying process.
- Year-round steady operation is possible.
Contact us to hear more about our solutions for pellet production
Do you want to hear more about Saalasti solutions? Contact us, and let’s discuss the needs of your production.
>> Read more about Saalasti High-Pressure Dewatering Press